Garage Door Manufacturing: ShockWatch RFID Case Study
Summary: The company needs to discover what was causing the product damage and eliminate all returns for which they could be liable
Product Solution: ShockWatch RFID
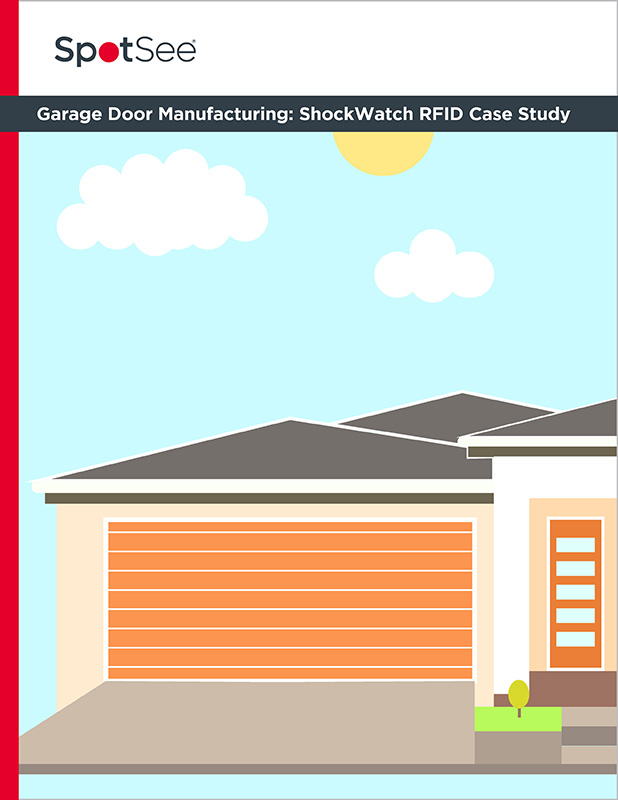
Read The Story
Garage Door Manufacturing: ShockWatch RFID
Application: Garage doors
Challenge: A garage door manufacturer was dealing with a large number of costly returns because customers were recieving damaged doors.
Goal #1 Discover what was causing the product damage.
Goal #2 Eliminate all returns for which they could be liable.
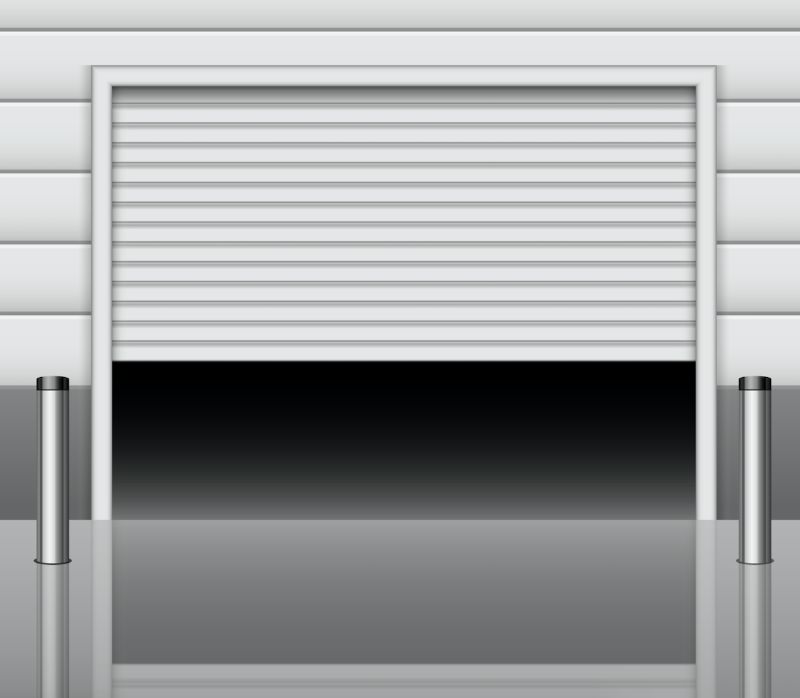
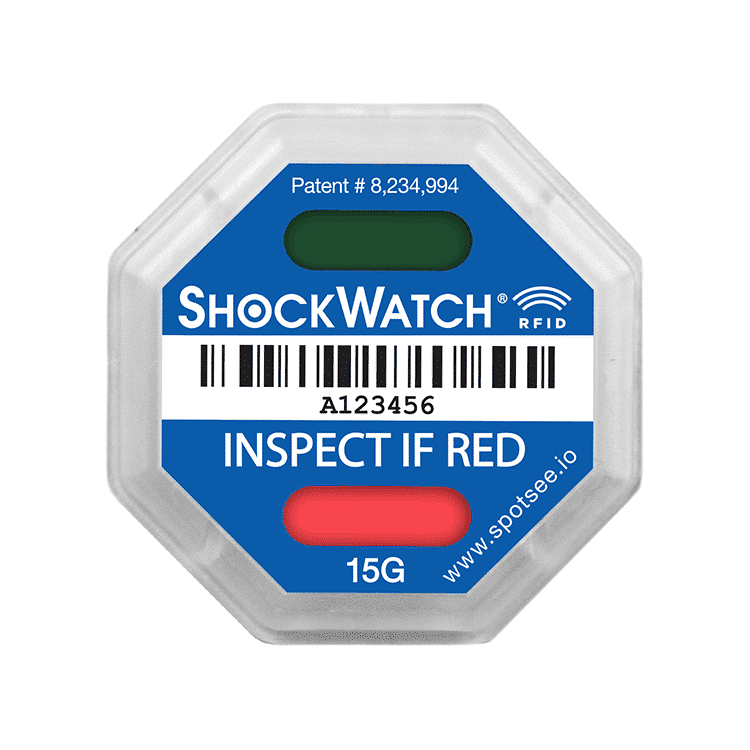
Product Solution
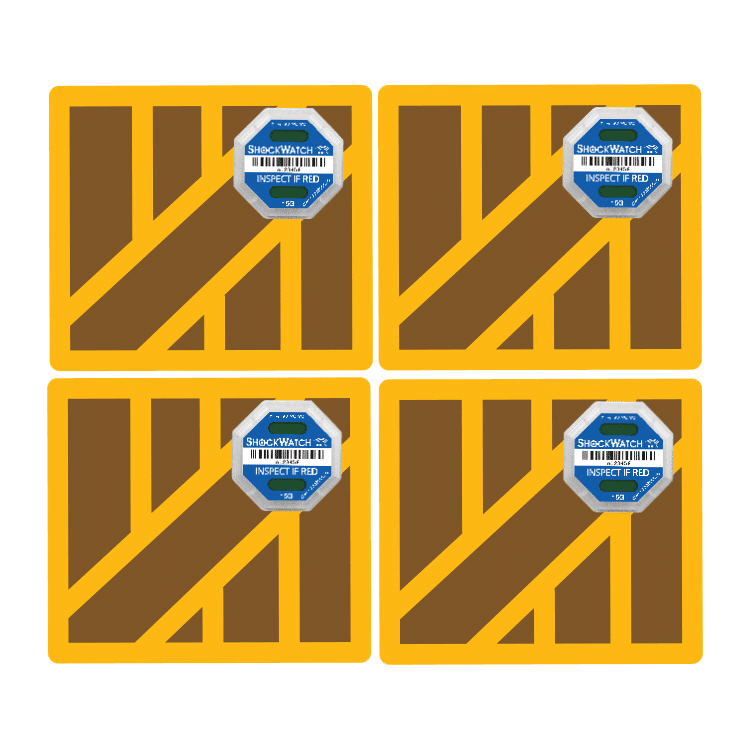
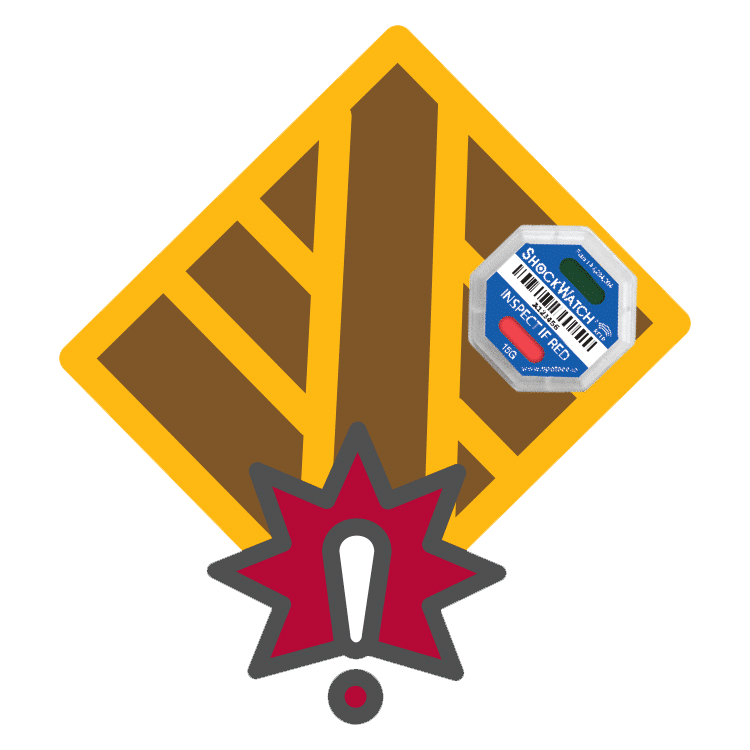
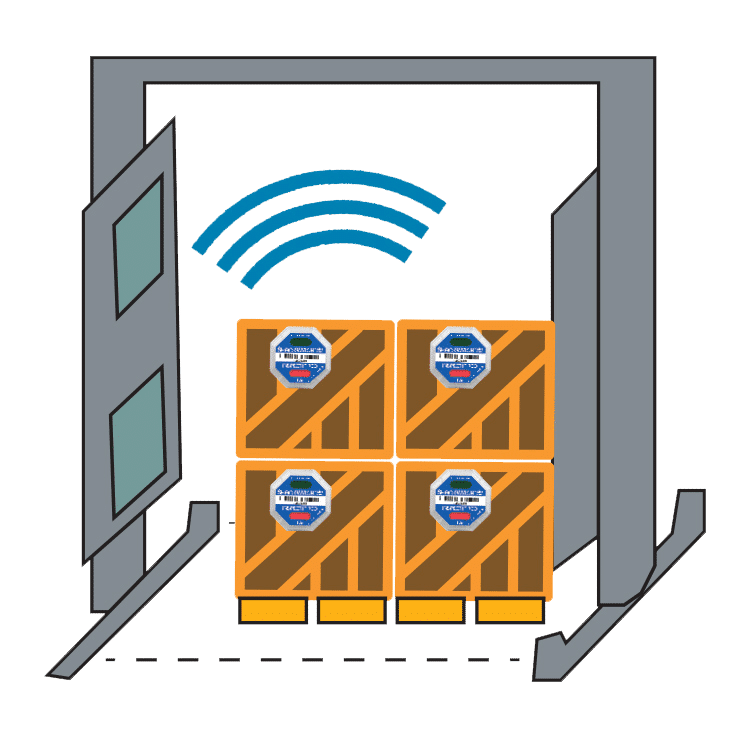
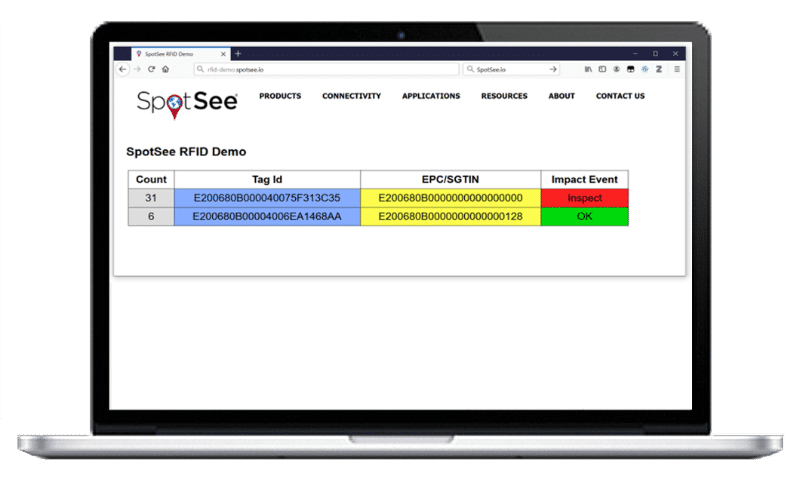
ShockWatch RFID is affixed to an asset
ShockWatch RFID will “activate”
ShockWatch RFID is scanned by a standard UHF reader
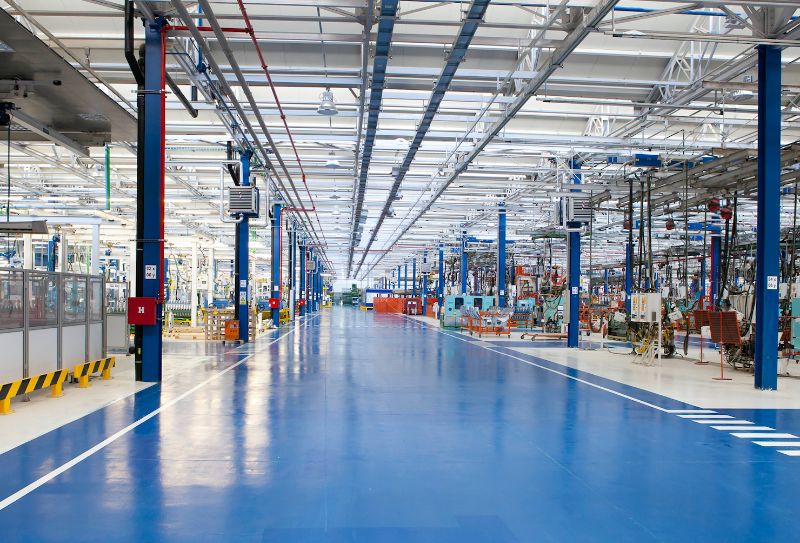
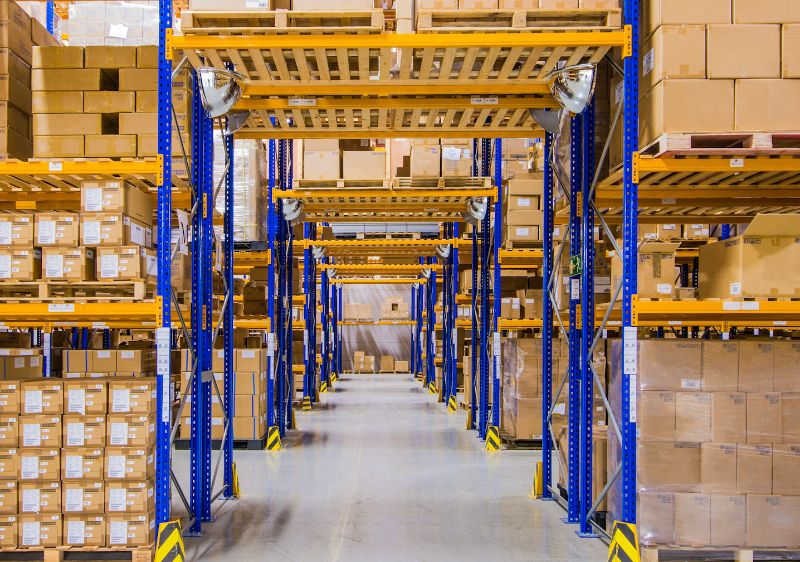
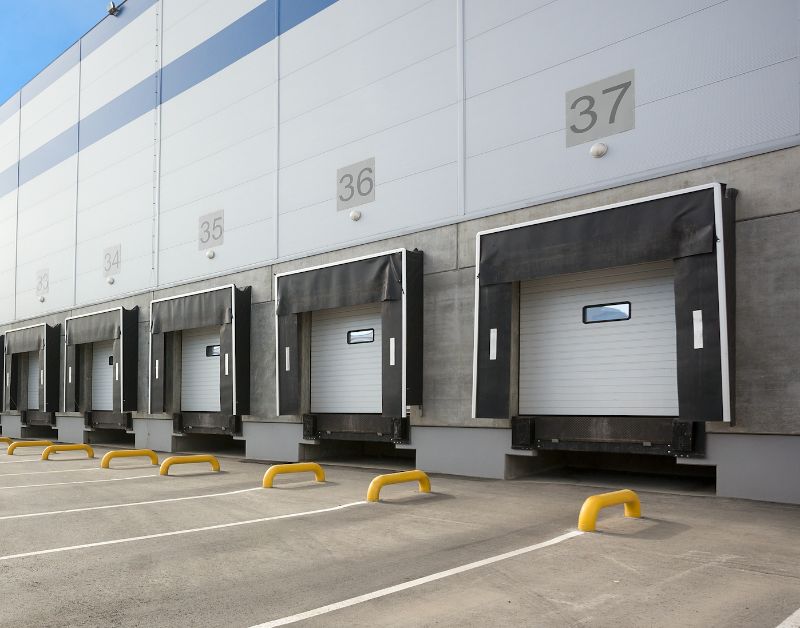
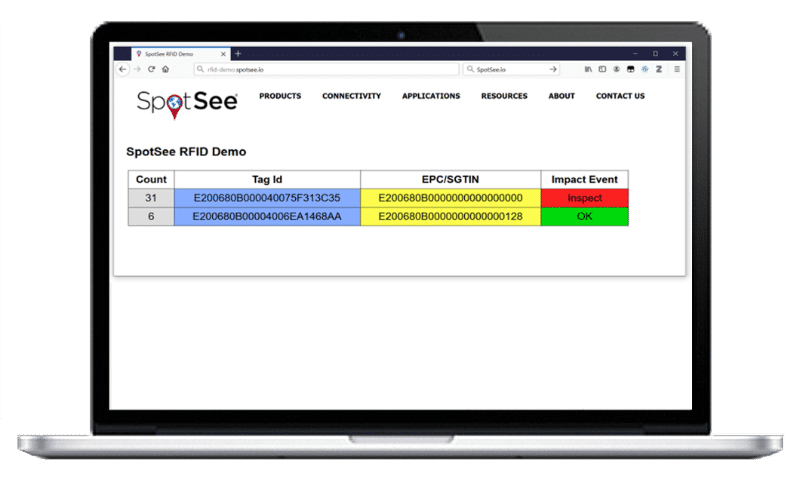
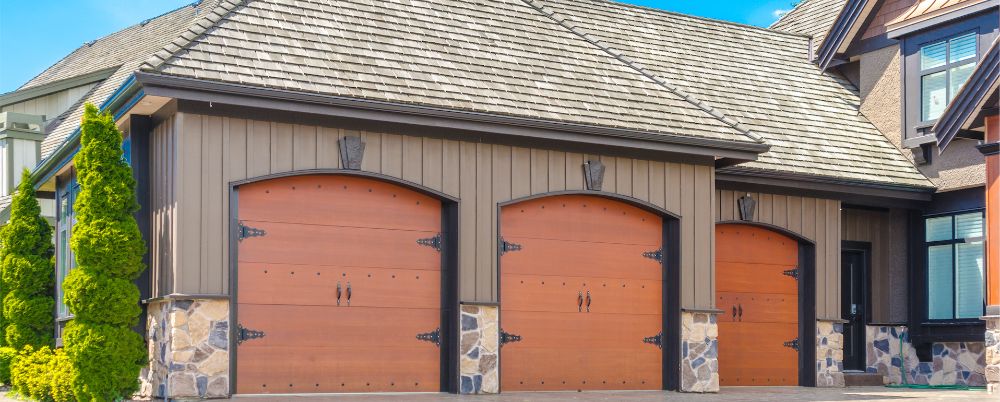
Extend the power of your RFID program by monitoring for damage
Every company wants to improve their supply chain processes. RFID technology aided companies in improving inventory control. The ShockWatch RFID impact indicator allows companies to leverage the inventory tracking benefits of RFID and the benefits of an impact monitoring program. With ShockWatch RFID impact indicators, the need for visual inspections during the receiving process is greatly reduced. When shipments are scanned, the receiver will know if there has been a potentially damaging impact. If the ShockWatch RFID has activated, inventory can be isolated for further inspection. If there has been no impact, the shipment can be moved into saleable inventory.
ShockWatch RFID impact indicators deliver all the benefits of an impact monitoring program – reduce damage from mishandling, refine supply chain processes so mishandling can be prevented, drive down costs – plus an electronic record of the information. Armed with data, it is possible to track down trouble spots in the supply chain and implement process changes to improve outcomes.
ShockWatch RFID impact indicators are single use devices that are tamperproof, field armable, turn red when an impact occurs and can be scanned with a standard UHF reader. Passive RFID technology is employed in the indicator so there is never a battery life issue to consider.
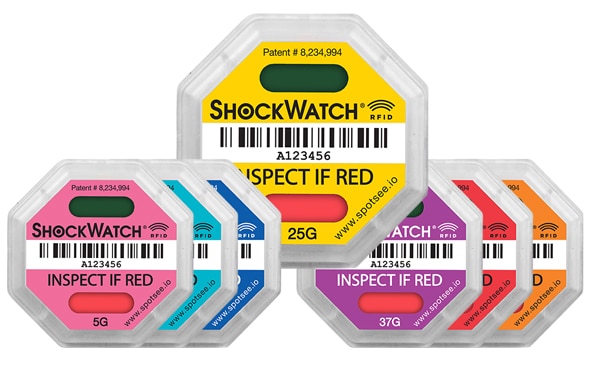
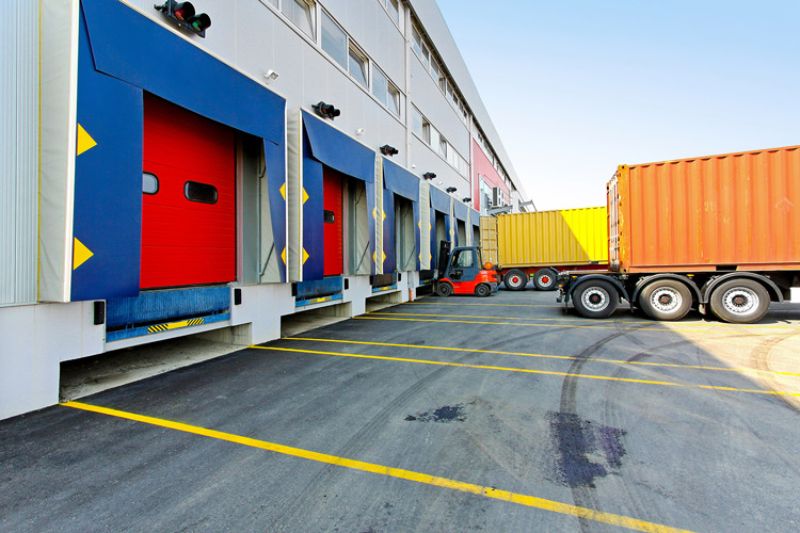
- Acts as a visual deterrent to mishandling
- Expands the utility of RFID with damage monitoring
- Reduces receiving times and isolates items that need inspection
- Reduces mishandling through awareness
- Helps identify trouble spots in the supply chain from production to transportation to storage