Pharmaceutical Manufacturing and Packaging Sourcer (PMPS) Article: “Finding the Right Temperature-Monitoring Device for your Supply Chain”
Finding the Right Temperature-Monitoring Device for Your Supply Chain
Mitigating against temperature deviations while shipping sub-zero COVID-19 vaccines has been vital to their safe delivery, but what solutions are best to stay on top of a product’s every move?
It takes years to get medications developed and approved. The process for creating a new drug includes multiple rounds of research, testing, evaluation, and assessment before being approved for use. The process is both labour and cost intensive, requiring hours of work and billions of dollars. At the end of the development process, there is a tremendous sense of relief as finally, after everything that was put into getting the medication approved, there is a tangible product that can be distributed. That’s when the next hurdle appears.
Part of the process for getting pharmaceuticals approved and in use is outlining steps for distribution, from the manufacturer all the way to the patient. As seen most recently with the COVID-19 vaccine, sometimes extreme temperatures are needed to ensure a product’s efficacy is maintained. Deviations, whether higher or lower than the set threshold, can significantly impact a product’s effectiveness, even potentially rendering it unusable. Unfortunately, the industry loses thousands, if not millions, of dollars annually, due to temperature deviations throughout the supply chain. Every year, over 68 million freeze-sensitive vaccines are shipped, and approximately 20% of those vaccines are accidentally frozen during transport or in storage. As a result, those 68 million vaccines are rendered useless. Thankfully, there are several solutions that organizations can implement to reduce the amount of temperature-related damage incurred during transit and storage.
Negative Impact of Temperature Issues
Implementing some form of monitoring program benefits the entire cold chain, from product manufacturer to patient. In addition to the billions spent developing a drug, it also costs a lot to manufacture and distribute the product. When products become unusable due to a temperature deviation, it creates a loss. The effort that went into creating the product, quality testing, packaging, and shipping doesn’t result in use: it results in waste. Furthermore, having to send a replacement adds more to the cost – return, replacement, and all the logistical efforts surrounding it. As a shipment makes its way through the supply chain, the next concern of a cold chain breach becomes accountability. If a shipment is mishandled by a specific party, it might be the responsibility of that party to pay for damages or replacements. Now, with ship-to-home therapeutics and medications, even the patient is part of the cold chain. If a product arrives and is not properly handled at the patient’s doorstep, unacceptable temperature exposure can ruin the product. Perhaps the worst thing about a breach in the cold chain is that without a monitoring program, the doctor, pharmacist, or patient may never know that there is an issue. Temperature-monitoring allows patients to feel confident in their medication, adds accountability to the supply chain, and, ultimately, saves those within the supply chain time and money.
Starting the Selection Process
Finding the right kind of device is crucial, but before identifying what kind of product will work best, it’s important to first identify the actual need. Does the pharmaceutical in transport require monitors for each individual vial or package, or will something that can be affixed to larger shipments work? Should the medication be monitored for temperatures that are too high, too low, or both? Does the product in question have specific needs that might be better met with a product- specific device like blood or vaccines? All of these are relevant questions to ask when considering the need and, in turn, in determining what solution might work best.
Once the need is understood, it can help narrow down a potential solution from a long list of options. For pharmaceuticals alone, the options range from single-use, time- temperature indicators, to full journey temperature recorders
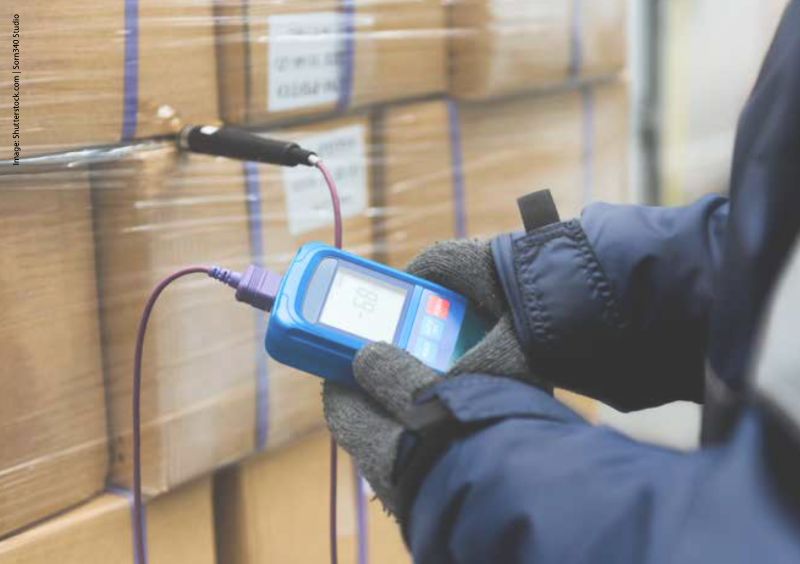
Time-Temperature Indicators
Time-temperature indicators can be used not only to alert users of exposure to unacceptable temperature conditions, but also to let the user know how long that temperature was experienced. Fluctuations in temperature can shorten the useable life of some medications while making others less effective, or potentially even dangerous. An example of a decrease in potency is insulin, the proper storage temperature for which is between 2oC and 8oC. If a vial were to experience a temperature of 25oC for a period of time, its shelf life would drop to about six weeks.
Even with careful, specifically designed packaging in place, issues may still occur. Packaging might experience damaging impacts, weather conditions could change, or unplanned shipping delays might occur, causing extended time between each cold chain checkpoint. Even once items have arrived at their destination and been stored appropriately, like vaccines in pharmaceutical-grade refrigerators, they may still experience temperature excursions. If the refrigerator malfunctions or the items aren’t handled properly, it could result in a loss of efficacy. Knowing if a cold chain breach has occurred and for how long, allows the end user – whether it’s a hospital, pharmacy, or a patient at home – to determine if products have been compromised. Colour- changing devices provide a simple indication of a temperature deviation. This option is easy to implement, and is an ideal solution for last-mile monitoring. The simplicity of interpreting the results makes them a logical choice when shipping directly to the patient.
Supply chain disruptions have become increasingly common, with shipments getting delayed due to weather, transportation issues, or even natural disasters
Temperature Recorders
Temperature recorders are typically more complex, and provide a complete record of temperature, as well as evidence of excursions. Not only do temperature loggers track and alert users to the condition of temperature-sensitive products, but they also provide an unchangeable record of it. Like temperature indicators, recorders can, and should, be used inside packaging to accurately track a product’s temperature. In addition to providing manufacturers, shippers, hospitals, and other administration with the same level of confidence as indicators – with the added layer of accuracy and detailed information – recorders can also provide insight into the overall cold chain. Recorded data might reveal trends among carriers or packaging issues. With that knowledge, steps can be taken to resolve existing issues and prevent future ones. If trouble spots are found, it may mean changing distributors or updating packaging to align with the season. However, recorders are not without their drawbacks.
Supply chain disruptions have become increasingly common, with shipments getting delayed due to weather, transportation issues, or even natural disasters. Once a shipment reaches its destination, how can usability and temperature maintenance be determined? Data loggers can be used to see if temperature fluctuations occurred. While recorders provide a complete temperature record, they are not well suited for shipment of medications to the home as they require a computer to download and interpret the results. They are also a more expensive solution so the cost/ benefit analysis must be considered.
IoT in the Cold Chain
New advances in technology, and new requirements from the Drug Supply Chain Security Act, are pushing the pharmaceutical supply chain to the next phase of supply chain management. The goal of the legislation is to drive greater transparency in the supply chain, and provide traceability from drug manufacturer to patient. Condition- monitoring, RFID-enabled solutions are beginning to find their place in logistics channels. With the implementation of RFID solutions, evidence of an intact supply/cold chain can become part of the drug’s permanent record. RFID solutions allow manufacturers and distributors to combine the benefits of RFID for inventory management, sensing technology for condition monitoring, and traceability from manufacturer to patient.
Other Conditions in the Supply Chain
While pharmaceuticals are most impacted by temperature changes, a common occurrence in any supply chain is physical damage. For organizations looking for a comprehensive view of their cold chain, there are condition- monitoring devices available. These devices not only monitor for temperature excursions, but also for damaging impacts and vibrations. Although the outside of a package might look unharmed, the inside might hold vials with microcracks or that are completely broken. Comprehensive monitors and loggers can leverage cellular connectivity to give users access to data at any time throughout a shipment’s supply chain journey. This accessibility gives logistics managers the opportunity to reroute shipments or schedule a replacement shipment if needed, ensuring products sent to the end customer aren’t damaged or unusable.
There are a wide range of options available to pharma manufacturers and distributors within the pharmaceutical supply chain. Understanding the need is the first step. From there, you can identify what type of product might work best, the number you’ll need given your shipment schedules, and how to monitor for deviations. Regardless of the option selected, having a temperature monitor in place creates a more transparent cold chain, allowing for the reduction of deviations due to mishandling, unreliable packaging, and a slew of other common causes. The result of implementing a temperature- monitoring device is a confident end user and, subsequently, a successful supply chain less burdened by additional costs brought on by damage.