Semiconductor Equipment Case Study: ShockWatch RFID
Product Solution: ShockWatch RFID
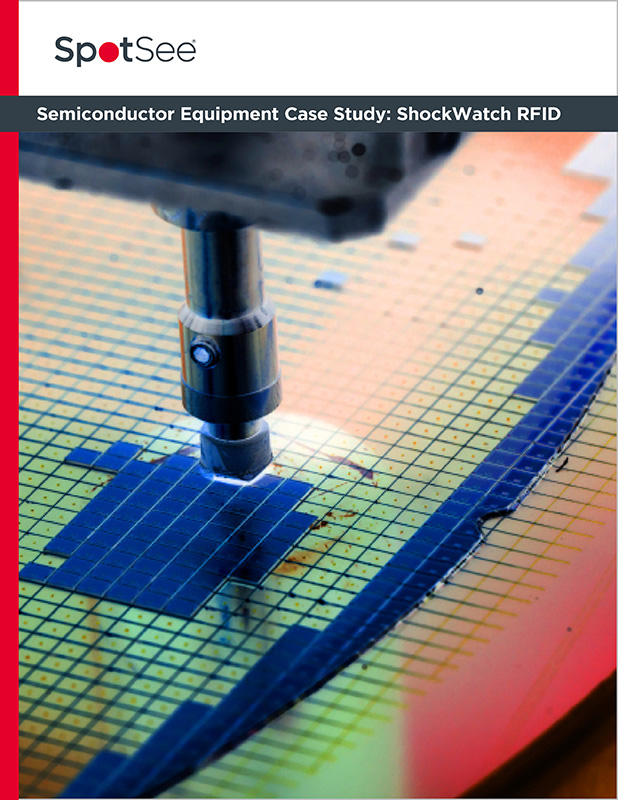
Read The Story
Semiconductor Equipment Case Study – ShockWatch RFID
Company Profile
Application: Fabrication Equipment and Silicon Wafers
Challenge:Semiconductor fabrication equipment and the silicon wafers they produce are extremely sensitive to impact and tilt.
ShockWatch RFID Tags Protect Sensitive Semiconductor Equipment and Wafers from Damage in Transit
Semiconductor fabrication equipment and the silicon wafers they produce are extremely sensitive to impact and tilt. To protect them during transport, many of the world’s largest manufacturers are beginning to use ShockWatch® RFID passive tags to monitor shipments and identify potentially damaging impacts.
RFID can make a noticeable improvement in terms of reducing damage rates for delicate wafers and the equipment that makes them. Given the current, global, shortage of semiconductor chips and growing global needs, taking extra steps to reduce damage is a logical precaution to protect your business.
It is a sound investment, too. SpotSee® partners report shipping damage was reduced an average of 50% when its highly visible impact monitoring tags were placed on their shipments. That’s because cargo handlers are more careful when they know someone is tracking the condition of the assets.
The semiconductor industry is faced by a two-fold challenge. Impacts, like being hit by shifting cargo during delivery, can fracture wafers. Stronger impacts, like being bumped by a forklift or dropped while loading, can damage fabrication equipment’s’ internal components.
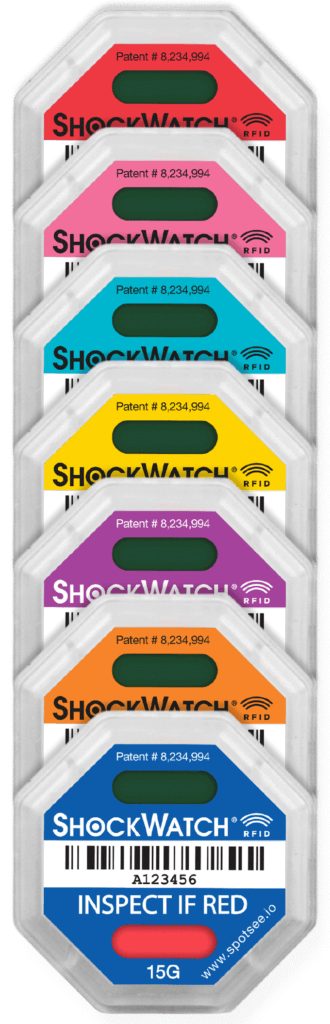
The Uptime Institute’s survey indicated 40% of outages cost their organizations between $100,000 and $1 million. As the survey showed, those costs are rising.
Gartner, a leading IT consultancy, noted two main areas of loss: Transactions that could be lost to time or competitors, and deleterious effects upon stakeholders. Unplanned downtime, therefore, gives customers a reason to chose another data center or cloud host.
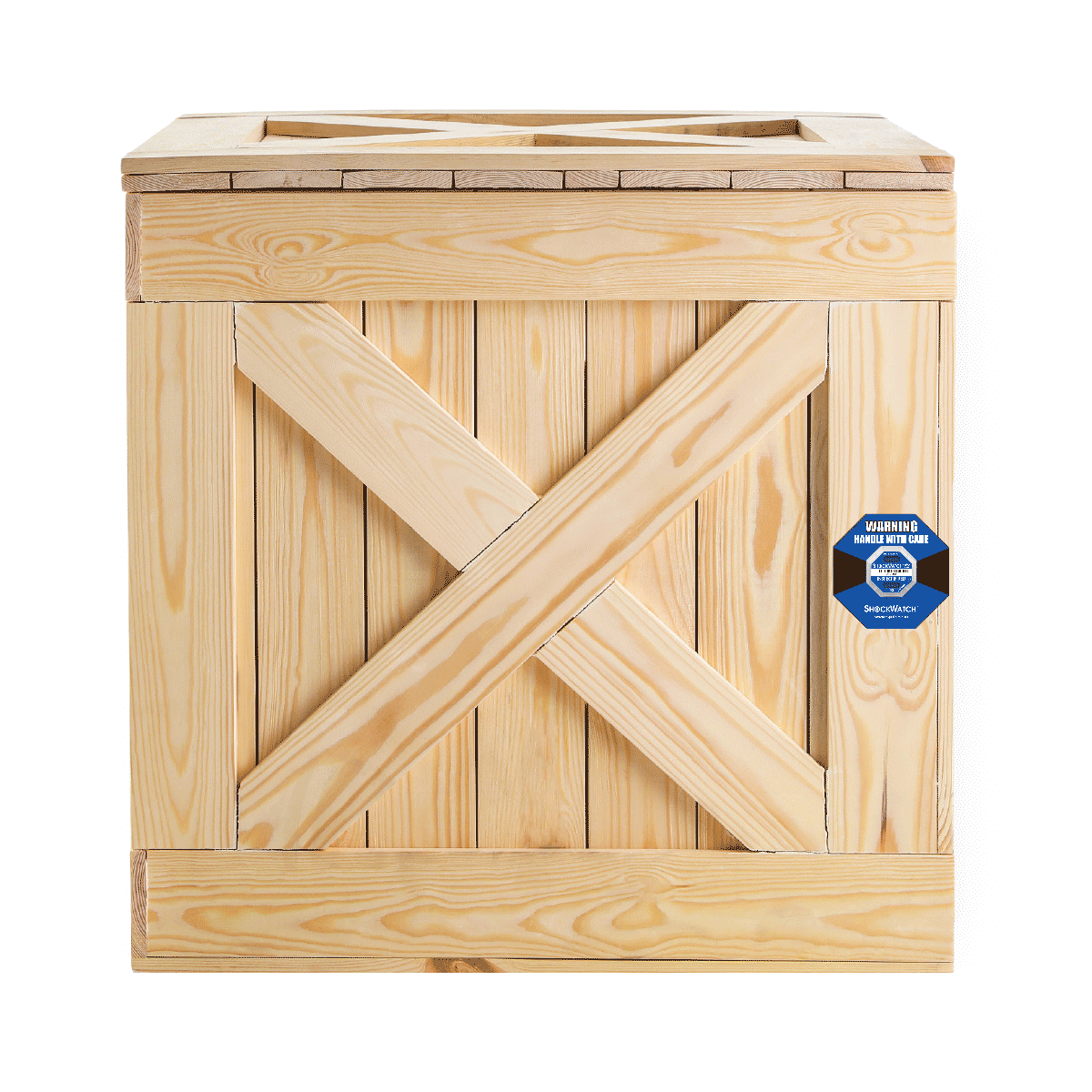
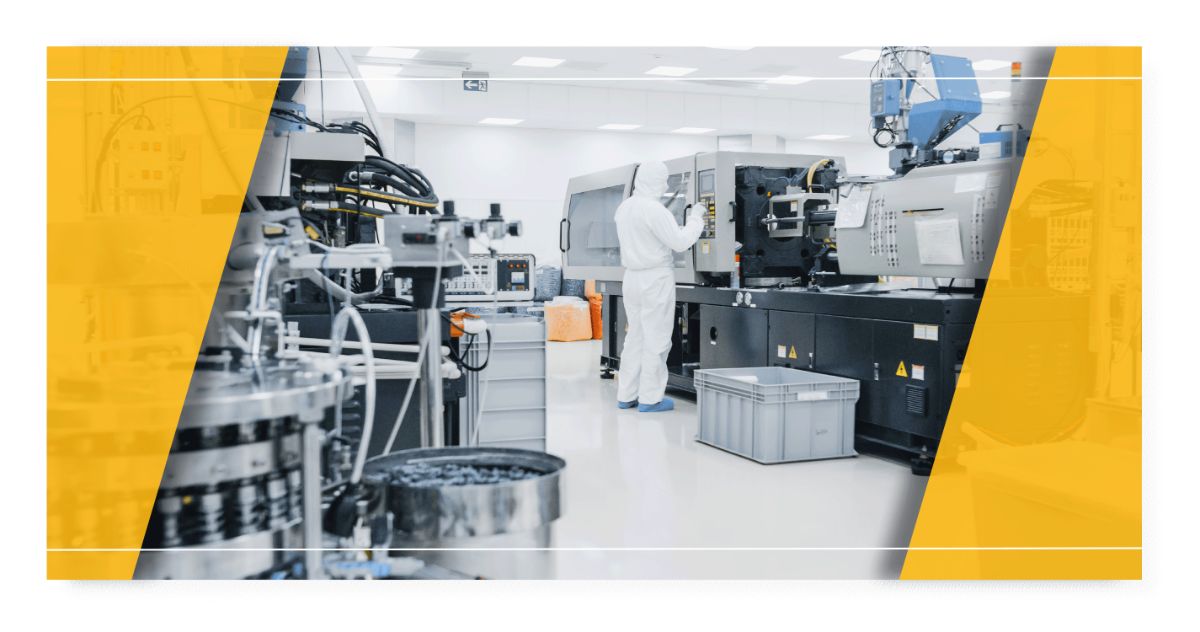
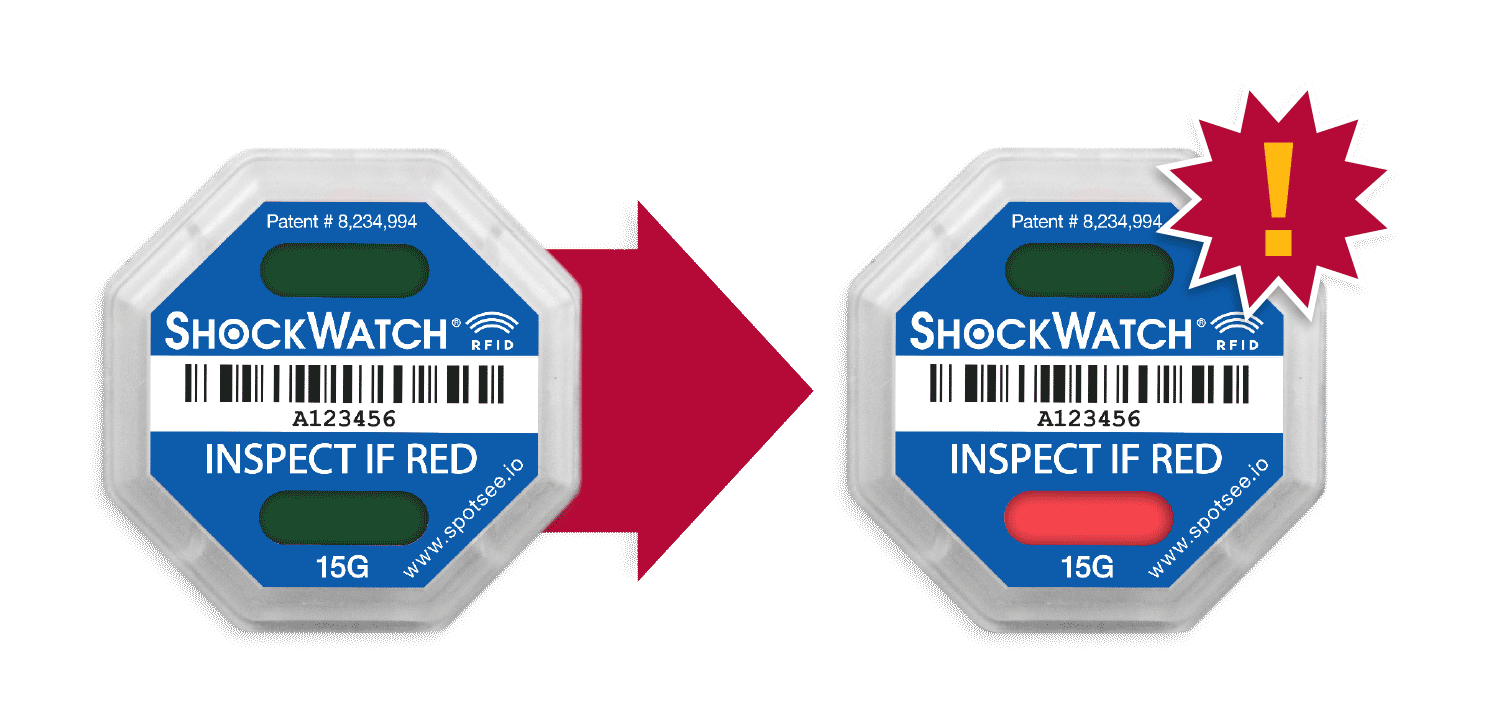
When RFID applications are linked to your inventory or equipment management system, condition reports are entered automatically when the equipment or wafers are received, and when they pass subsequent scanners as they move deeper into your facility. Importantly, today’s RFID technology doesn’t require line-of-sight to be read, and readers can read hundreds of tags in a few seconds.
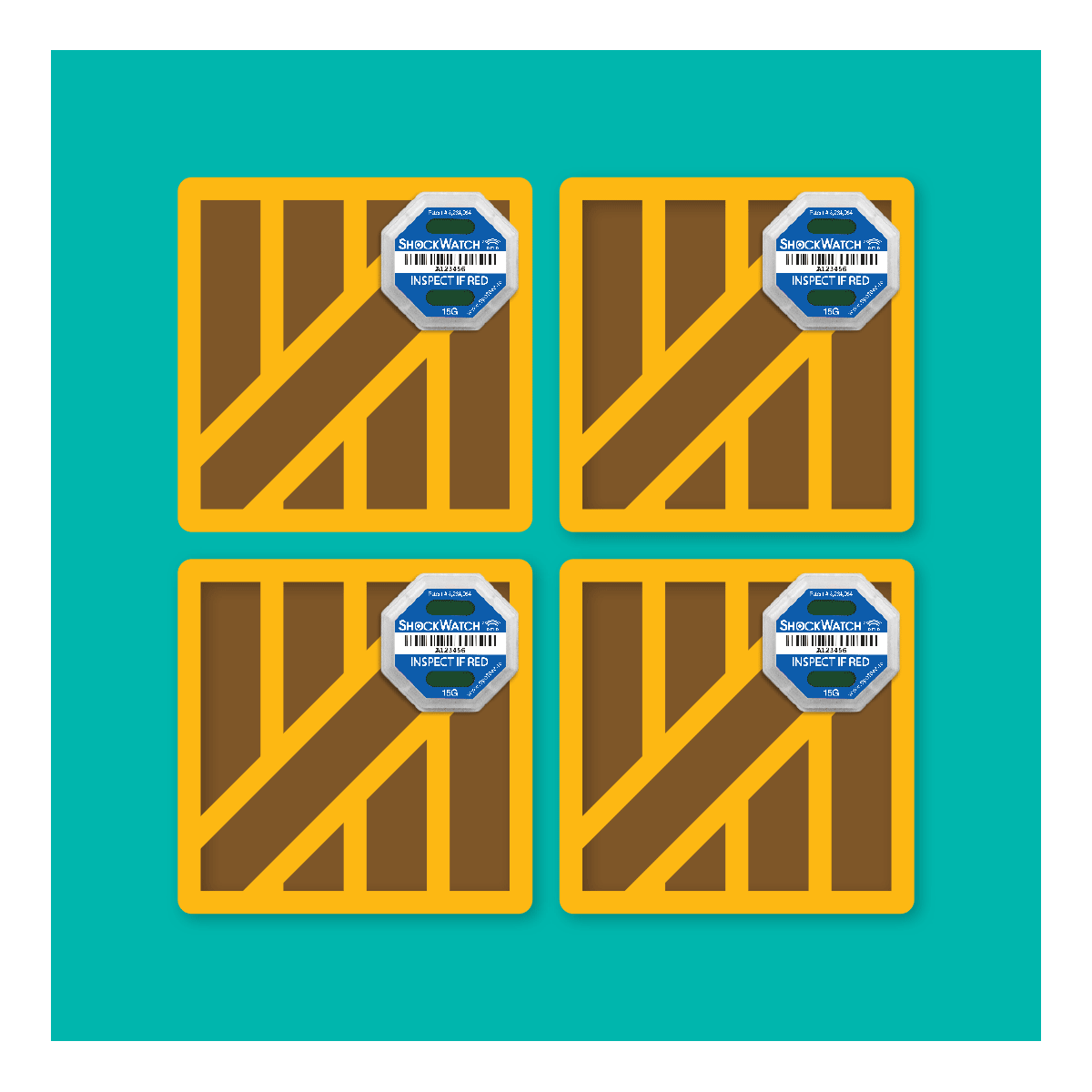
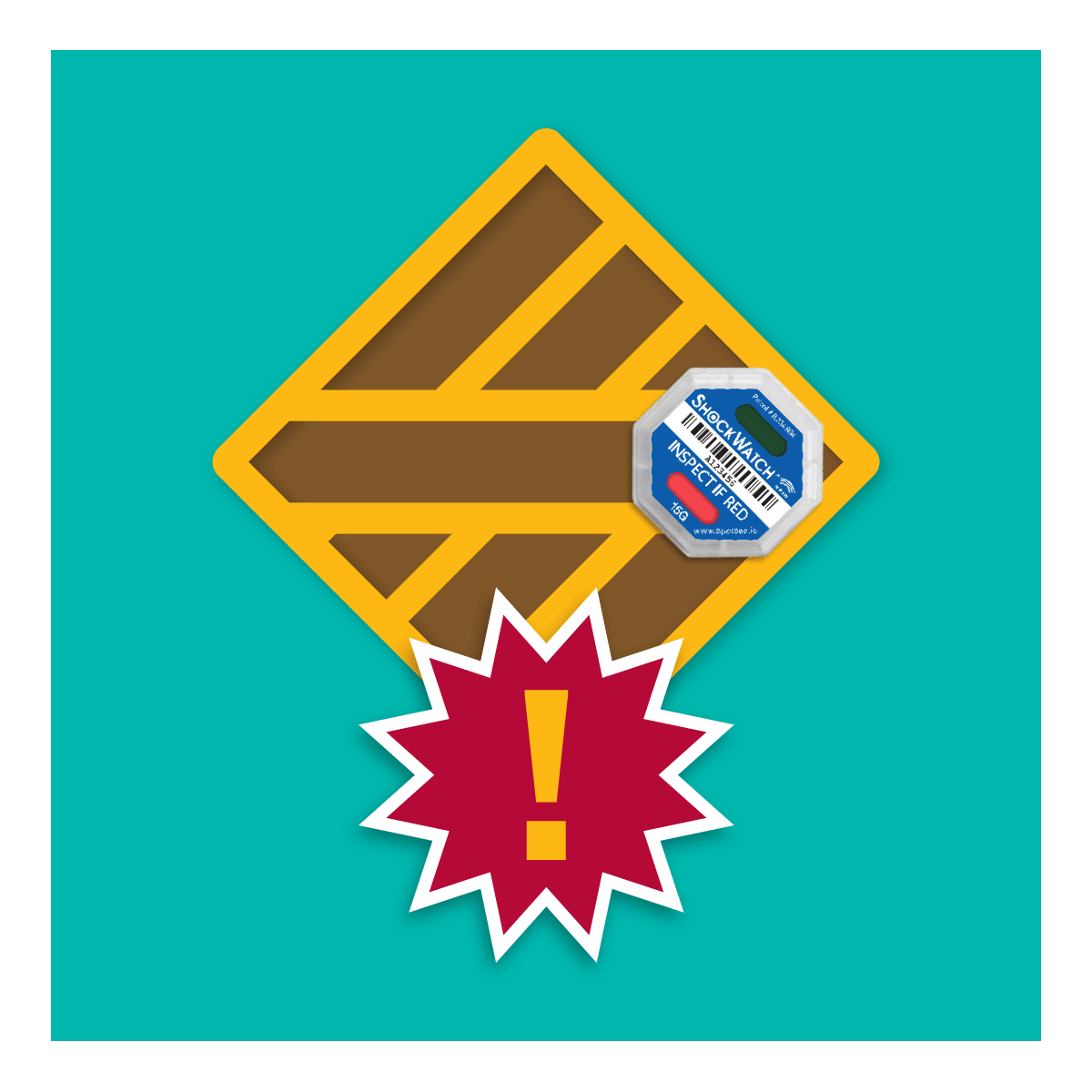
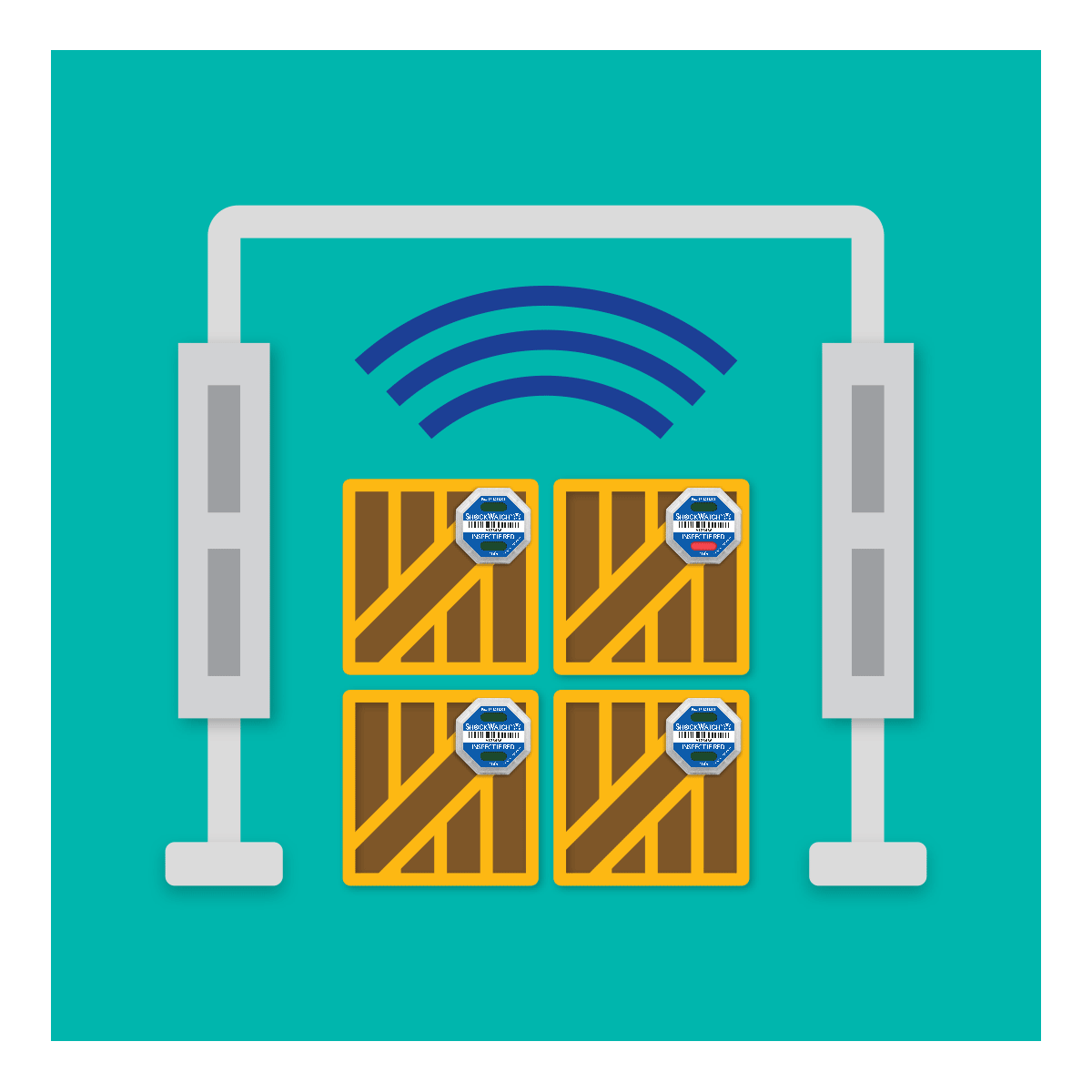
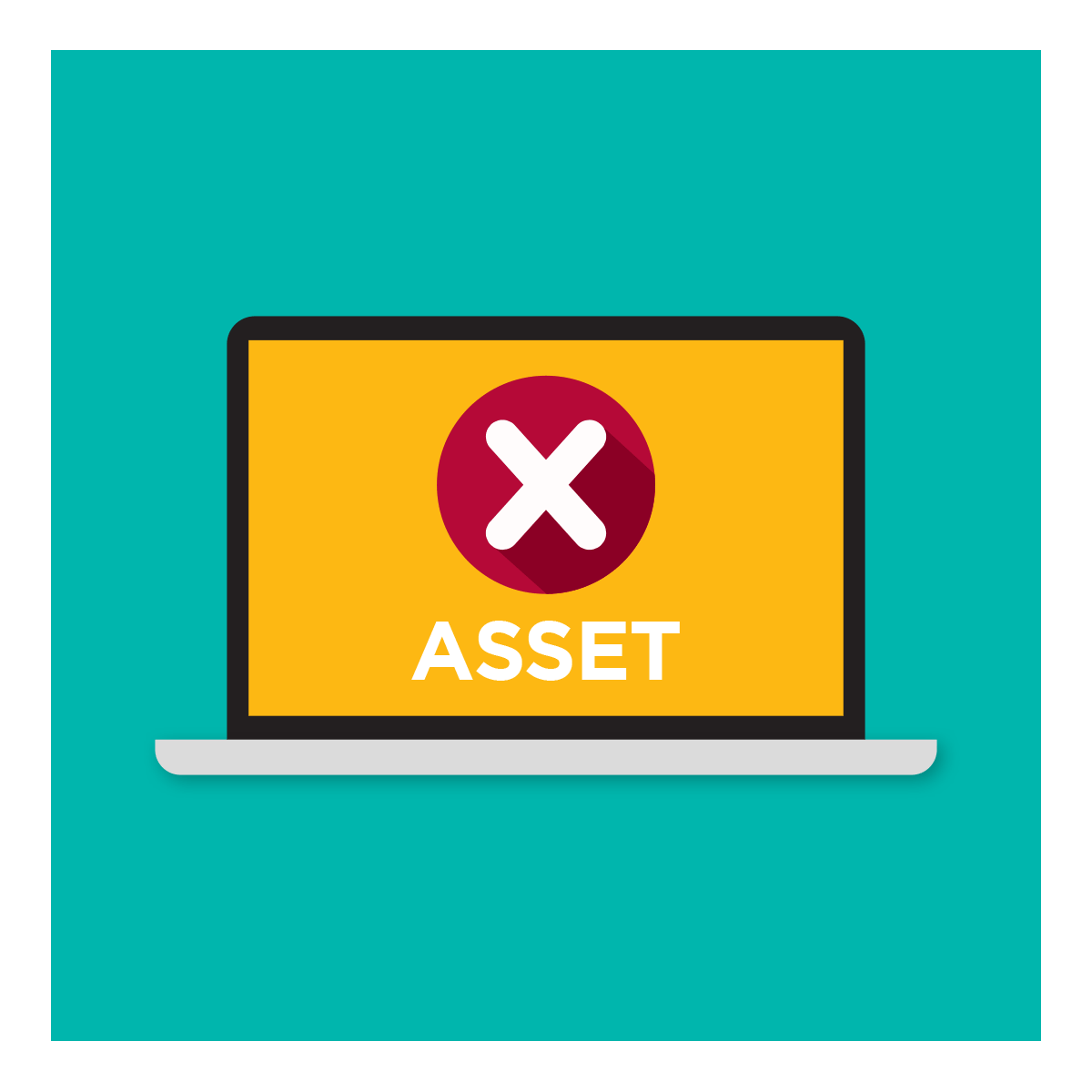
ShockWatch RFID is affixed to an asset
ShockWatch RFID is scanned by a standard UHF reader
Royal Philips Electronics became the first major semiconductor fabricator to deploy RFID tags throughout its semiconductor division in Asia in 2005. Since then, others have started adopting this technology to gain visibility into their supply chains and their own manufacturing environment. Now, RFID is making inroads throughout the supply chain, too, providing greater visibility into the condition of sensitive items throughout their transit.
Preventing damage and learning about damage to your equipment and materials early, before they are in the production line, are part of a comprehensive loss reduction plan that can help you avoid delays that could damage your reputation and drive customers to competitors. Using visible monitors, like SpotSee’s ShockWatch RFID tags, goes a long way towards preventing shipping damage.
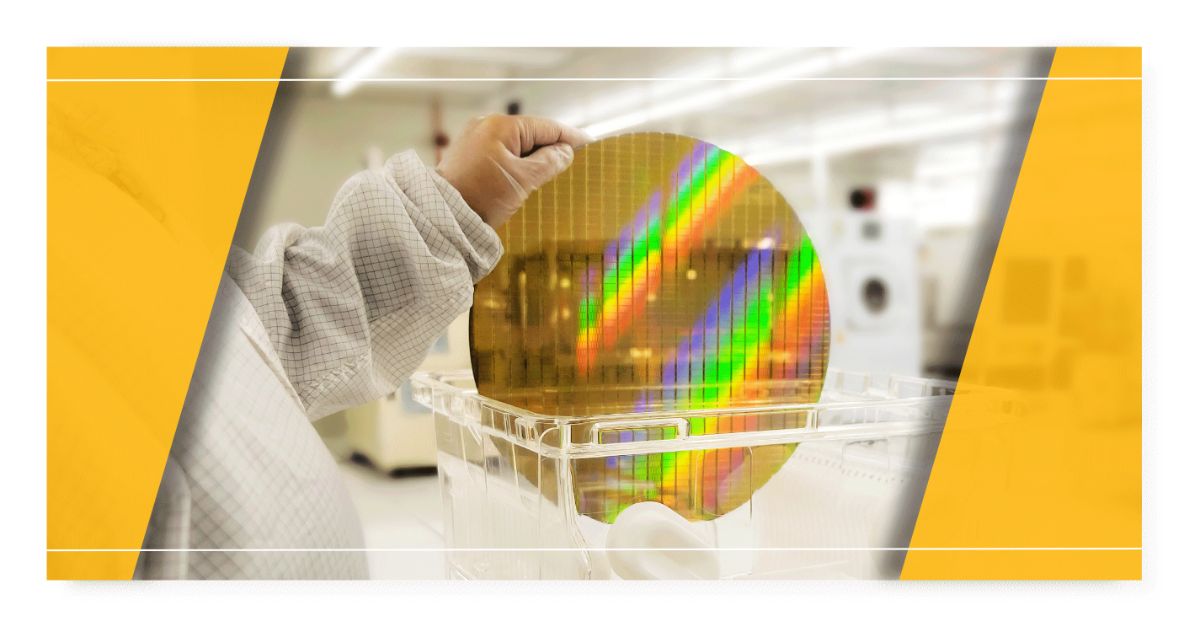
Extend the power of your RFID program by monitoring for damage
Every company wants to improve their supply chain processes. RFID technology aided companies in improving inventory
control. The ShockWatch RFID impact indicator allows companies to leverage the inventory tracking benefits of RFID and
the benefits of an impact monitoring program. With ShockWatch RFID impact indicators, the need for visual inspections
during the receiving process is greatly reduced. When shipments are scanned, the receiver will know if there has been
a potentially damaging impact. If the ShockWatch RFID has activated, inventory can be isolated for further inspection. If
there has been no impact, the shipment can be moved into saleable inventory.
ShockWatch RFID impact indicators deliver all the benefits of an impact monitoring program – reduce damage from mishandling, refine supply chain processes so mishandling can be prevented, drive down costs – plus an electronic record of the information. Armed with data, it is possible to track down trouble spots in the supply chain and implement process changes to improve outcomes.
ShockWatch RFID impact indicators are single use devices that are tamperproof, field armable, turn red when an impact occurs and can be scanned with a standard UHF reader. Passive RFID technology is employed in the indicator so there is never a battery life issue to consider.
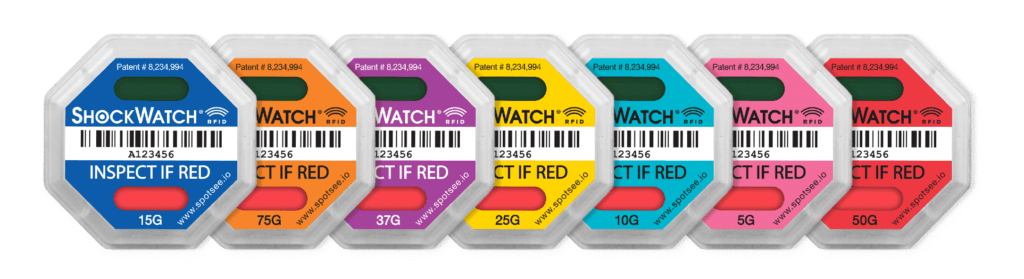
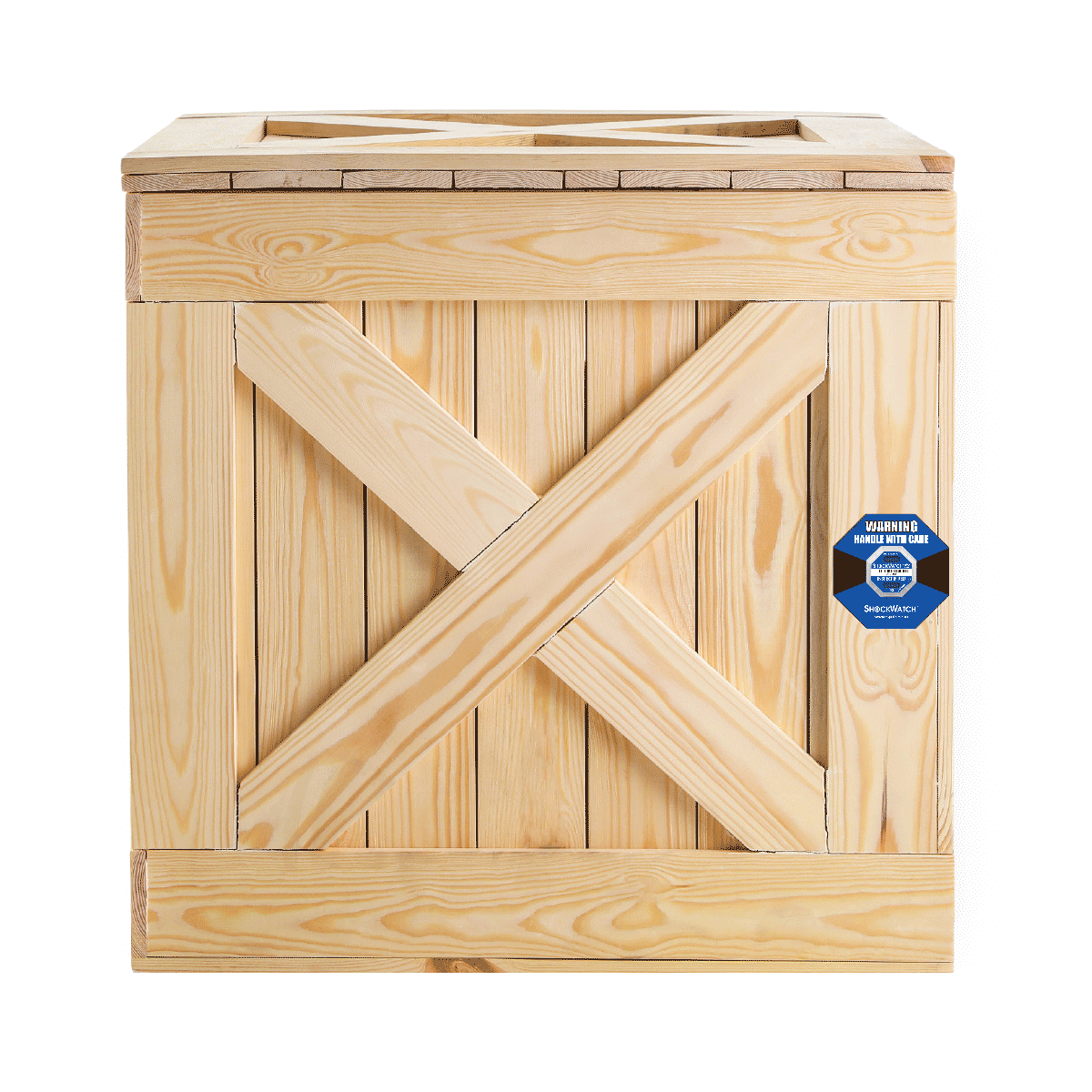
- Acts as a visual deterrent to mishandling
- Expands the utility of RFID with damage monitoring
- Reduces receiving times and isolates items that need inspection
- Reduces mishandling through awareness
- Helps identify trouble spots in the supply chain from production to transportation to storage